Mechanical Forging Presses
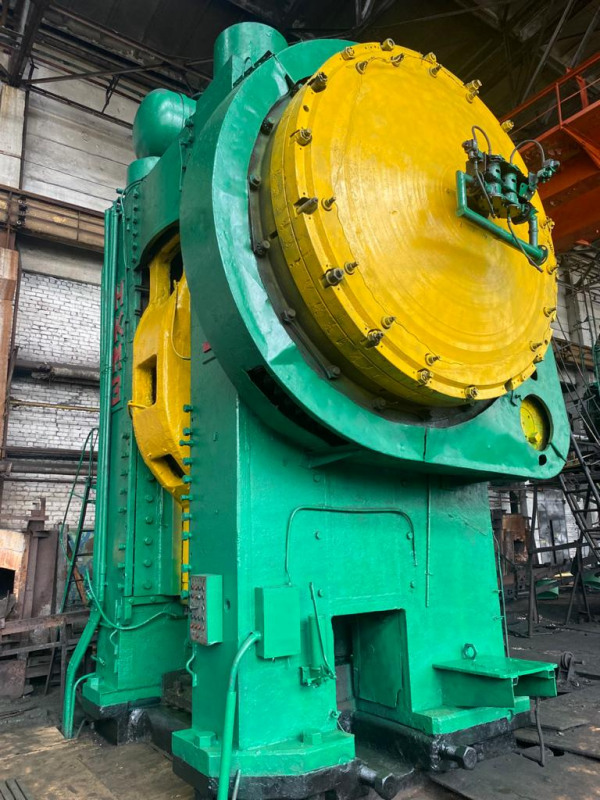
Zhengxi is a professional manufacturer of hydraulic presses in China, and a designer and builder of high-quality mechanical forging machines.
A mechanical press converts the rotational force of a motor into a translational force vector that performs a pressing action. Therefore, the energy in a mechanical press machine comes from the motor. These types of presses are generally faster than hydraulic or screw presses. Zhengxi's mechanical forging presses provide the highest level of efficiency in the following areas: Warm forging (part temperature from 550 to 950°C) and hot forging (part temperature from 950 to 1,200°C)
Unlike some presses, in a mechanical press, the speed and magnitude of the applied force vary throughout the stroke distance. The correct range of travel is critical when performing manufacturing operations with mechanical presses.
Mechanical press machines are commonly used in metal forging fabrication and sheet metal fabrication. The required force application will determine the type of machine required. Squeezing generally requires more consistent force over longer distances.
Mechanical presses are usually a good choice for impact extrusion. Because the rapid and repeatable application of force over a limited distance is required for this type of manufacturing process. The most powerful mechanical forging presses in modern manufacturing have a press capacity of approximately 12,000 tons (24,000,000 lbs).
Working Principle
Mechanical forging presses are powered by a motorized flywheel. The flywheel transfers energy to a piston. The piston slowly applies pressure to the mold.
The machine is forced down by the motor and controlled by the air clutch. During the stroke, the crankshaft of the press applies constant, consistent pressure to the punch. This is similar to the shape of pressing clay into the palm of your hand. Speed does not equal power. The press will be fastest in the middle of the stroke before the density of the metal is highly compressed. It does not reach maximum pressure until the end of the stroke, pressing the workpiece into its final shape.
Since the mechanical push rod moves a fixed distance, when you are using a press make sure the closure at the end of the stroke is not too small so the push rod does not stick to the die at the bottom of its stroke.
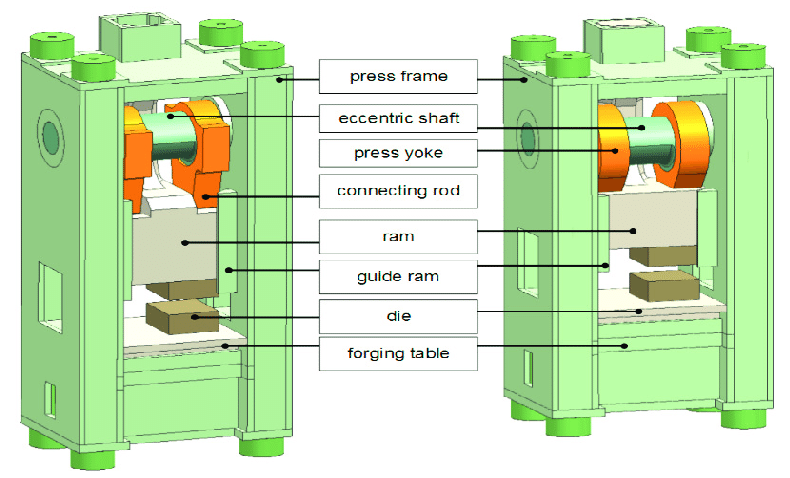
Features of Mechanical Forging Press
- Wide variety of parts and high productivity.
- Using nominal pressures from 2,500 kN to 20,000 kN, the widest possible range of part geometries can be produced using both warm and hot forging.
- Advanced drive kinematics and high-performance bedside and slide-side ejectors provide ideal conditions for reliable parts handling and high productivity.
- Optimum part quality and long tool service life.
- The mechanical forging press frame is of extremely robust welded design.
- Its compact construction and 2-point sliding suspension allow high stiffness and high levels of eccentric loads.
- Extremely precise slider guides.
- The generous mold space provides enough room to integrate complex multi-station molds with 5-6 forming stations. Such a large number of forming stations enables more precise forming of complex geometries.
- Even narrower part tolerances can be achieved with optional sizing/calibration operations.
- Low maintenance and user-friendly. The design, execution, and control software of the Zhengxi press series is very user-friendly. This ensures short start-up and changeover times as well as less service and maintenance time.
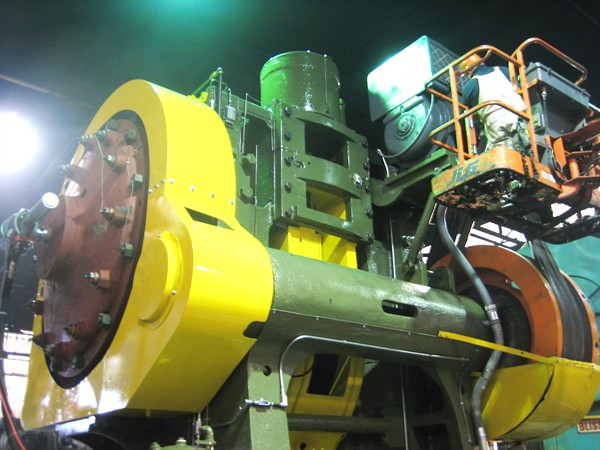
Our Mechanical Forging Presses Advantages
- High output rates
- Optimal quality
- Wide range of parts
- Long stroke length
- Minimum contact times
- Extended non-contact times for die cooling
- Long die life
- Large die space
- Tight component tolerances and high component quality
- Optional servo drive
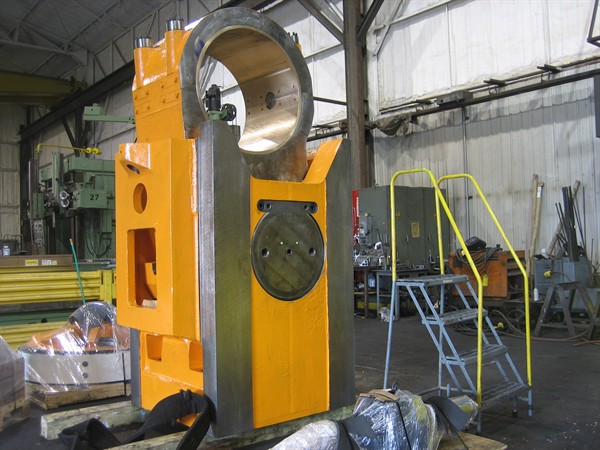
Application of Mechanical Forging Press
Due to the high cost, mechanical forging presses are only worthwhile for high-volume applications. For example, they are widely used in the automotive industry to produce and mold drivetrain parts. Governments also used them for coinage.